| |
Injection |
|
At first glance, injection appears to be a handy remedy
for a number of board ailments, easily accomplished with a minimum of
tools in the privacy of your garage. Invariably, though, the process is a
blind one, with us wishing the injected material to go where needed - but
suspecting that it will not necessarily comply with our wishes.
And then there is the compatibility to consider of
the injected material versus the material it is intended to reinforce.
And then there are the problems inherent in
injecting exothermic materials into insulating material with a low melting
point |
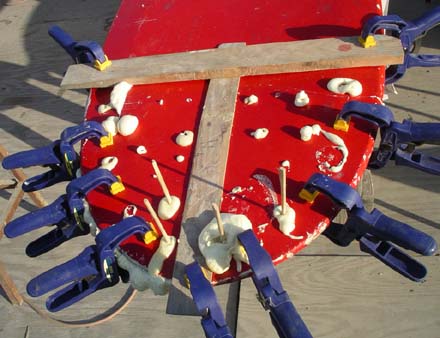 |
Injection most often comes up in connection with soft
decks. As per the cross-section at right, soft decks are caused by
disintegrated EPS foam, often closely followed by failed PVC sheet foam
(do the crunch test as described on the soft
decks page to see just what ails you) |
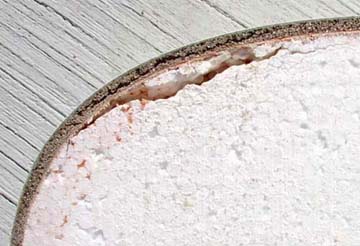 |
For injected material to make a meaningful structural
contribution, it must have similar mechanical properties to the material
it is intended to reinforce. We are concerned
here with EPS, a soft, spongy material that compresses readily, and
returns almost as readily to its original shape - for a while, anyway.
We are also concerned with PVC sheet foam (Divinycell
etc), that can flex a great number of times without ill effects.
Into all of this you want to inject - Epoxy resin??
with all the flexibility of a brick... Exactly what good could it do?? It
would sit wherever it happened to end up, rigid and unyielding, surrounded
by an ever-flexing collection of materials. They would shortly part
company, to each continue in its own way - with the only noticeable change
being an increase in board weight. |
And then there is the exotherm: the Epoxy blob at
right is the result of injecting West System 105/206 (the slow variety)
into a neat 1/8" dia hole I had drilled into the EPS. The Epoxy puddled,
melting a cavity for itself, wherein it sits, doing exactly nothing but
look silly. Judging from the black edges,
this got hot enough to have smoldered! |
 |
But here is 2-part Marine Urethane foam, injected into another 1/8" hole:
it traveled beautifully into open EPS foam channels, reinforcing same as
it went - and nothing melted in the bargain! While not
having totally the same mechanical properties as EPS, this Marine Urethane
foam is at least similar, with similar density, and ability to flex and recover.
Now THIS makes sense! |
 |
 |
 |
In order to make sure it goes into all
EPS cavities, I drill 1/8" holes approx 2" apart, start injecting small
batches (10cc admixed) from the rail inboard, then skip those holes that have already
had Urethane foam spill out of them. |
Once mixed, Urethane foam will wait for
no man, so preparation is the key to success. Use a stopper of sorts
(finger, syringe) during foam expansion, to encourage foam migration into
the board. And be prepared for a bit of a mess! |
Regarding the failed PVC
sheet foam, I have never been able to control Epoxy resin injection well enough to
guarantee a useful glue line (and believe me, I have tried, hoping to be
able to cut my turn-around times). After many experiments I have come to
the conclusion that the only predictably successful repair is replacement of
the PVC sheet foam. So very sorry!
at right the unhelpful injection of
filler I found in the soft deck of a race board |
 |
back
to Repair Menu |
|